Say you had the opportunity to design a distillery from scratch. The world is your oyster in terms of equipment and style, but you have to build a viable business.
Would you want a giant floor for malting barley the traditional way, or would you save the space and buy your malt in bulk? Would you go for a plump copper pot still, or something more sleek and efficient, like a Coffey still? And what kind of architecture? Something idyllic and homey, like a hobbit burrow, or perhaps something more modern and industrial?
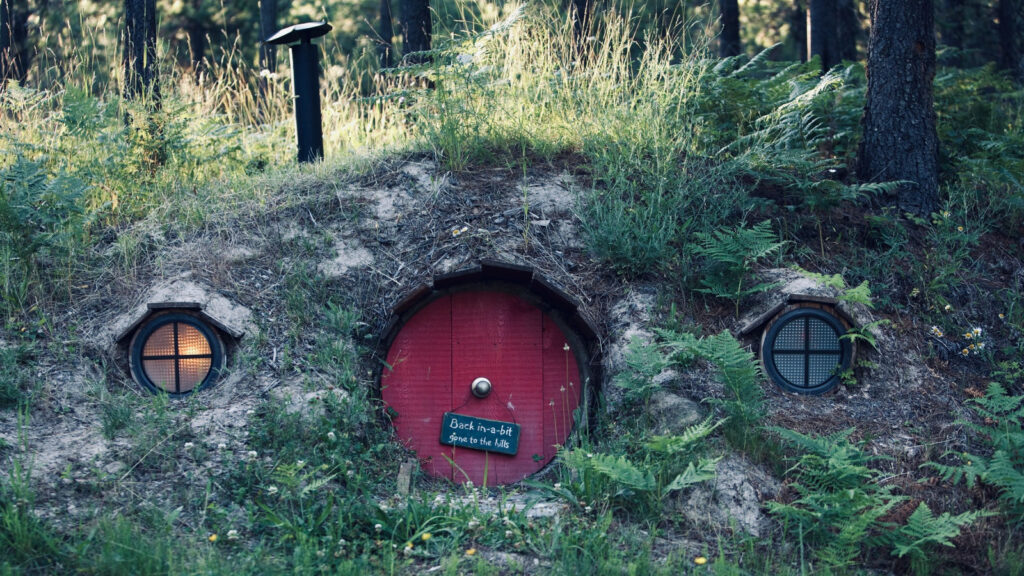
These were just a few of the many questions we had to answer when designing the architecture for Nine Rivers Distillery. Ultimately, we wanted to build something that was fit for purpose as both a functional and efficient distillery, while also providing a safe and engaging environment for visitors.
Distilling from the shoulders of giants
In 19th century Scotland, no one gave a second thought about visitors’ centres, on-site shops, or stampedes of whisky lovers who wanted to see how the proverbial sausage was made.
Historically, distilleries were industrial facilities. They were designed for five simple tasks: malting barley, milling grains, mashing, fermentation, and distilling spirits (the drinkin’ kind, not the oogie-boogie kind, although apparently there are quite a few haunted distilleries around the world).
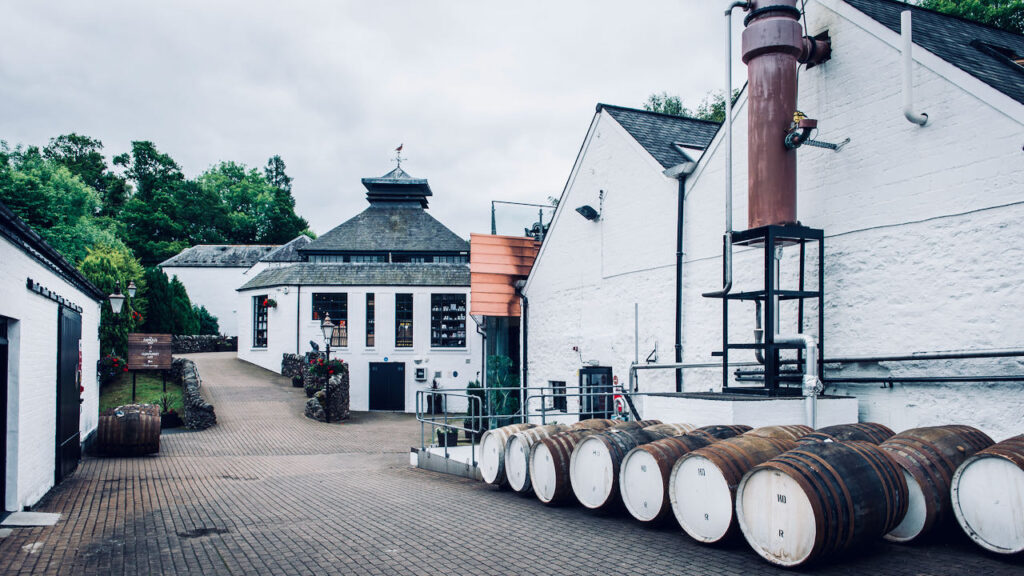
They were notoriously dangerous places that most people in their right mind wouldn’t want to visit. Of course, even at our best, most whisky lovers – ourselves included – aren’t in their right minds, so whisky tourism grew to be a thing.
We have Glenfiddich to thank for that. They laid claim to the world’s first distillery visitor center back in 1969, and while several decades passed before the idea took off, the expectation for a hands-on learning experience has since become the norm.
So much so, in fact, that most distilleries have stopped malting their own barley, and have even started shipping out their casks to offsite dunnages to make more room for retail tourism. It makes sense, given that Scotland alone saw about 2.2 million visits to Scotch distilleries in 2019.
Striking the right balance between function and flair
For Nine Rivers, we’re definitely looking to create an environment and experience that will attract whisky lovers from around the world, which is why we invested so much time and effort into choosing the perfect site. At the same time, we have a few other priorities that we hope to balance with the business side of things.
For one, there’s quality and tradition. Instead of hopping on the malt-less bandwagon like all but six Scotch distilleries have done in recent years, out of commitment to our craft we want to keep everything in-house, from grain to glass. That will give us greater control over the end product and help us produce something that’s truly unique. So we decided to include plenty of space for traditional floor malting and cask storage.
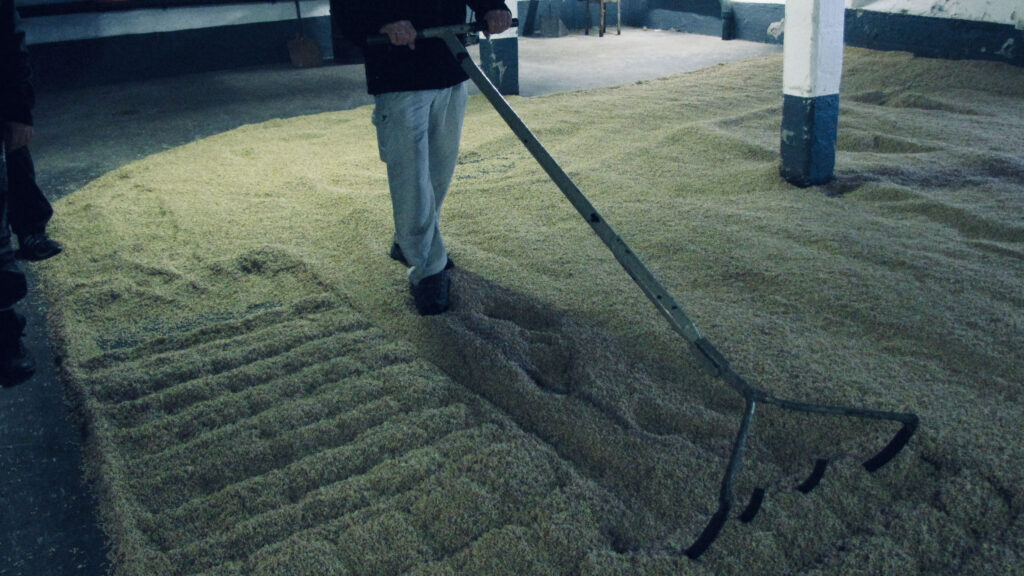
Second, we want to limit our impact on the environment. Nature provides the raw materials that define our whisky, and nine clean rivers are a lot more appealing to us than nine rusty troughs of old pot ale sludge. We assume the same goes for our customers, so designing a site that uses less energy and produces less waste was an important priority.
Site design has a definitive impact on how water is used and re-used, how stills are heated and climate is managed, and how spent grains are recycled. We’ve since done a lot of innovative work in this area and will share more at a later date.
Finally, we want to integrate with the local community. In terms of look, feel, and impact, we wanted to highlight our own cultural heritage while paying proper respect for local norms and expectations. More about this in just a moment. But brace yourself because it involves a fair bit of Feng Shui.
Finding partners who can bridge east and west
Not just any architecture firm would cut it. We wanted to make a striking visual impact – a strong western statement that pays homage to traditional craftsmanship. And yet we needed a partner with deep roots in architectural and construction projects in China.
Aesthetics aside, China’s rules and regulations for buildings – especially facilities that make anything for human consumption – are among the strictest in the world, and without someone who understands how things work here, there’s no way we would have secured the license and permission to build.
Enter SOG design
We began our search for an architectural design firm back in early 2020. This was right in the middle of serious intercity lockdowns, so like everyone else we were heavily reliant on video conferences. (Our favorite!)
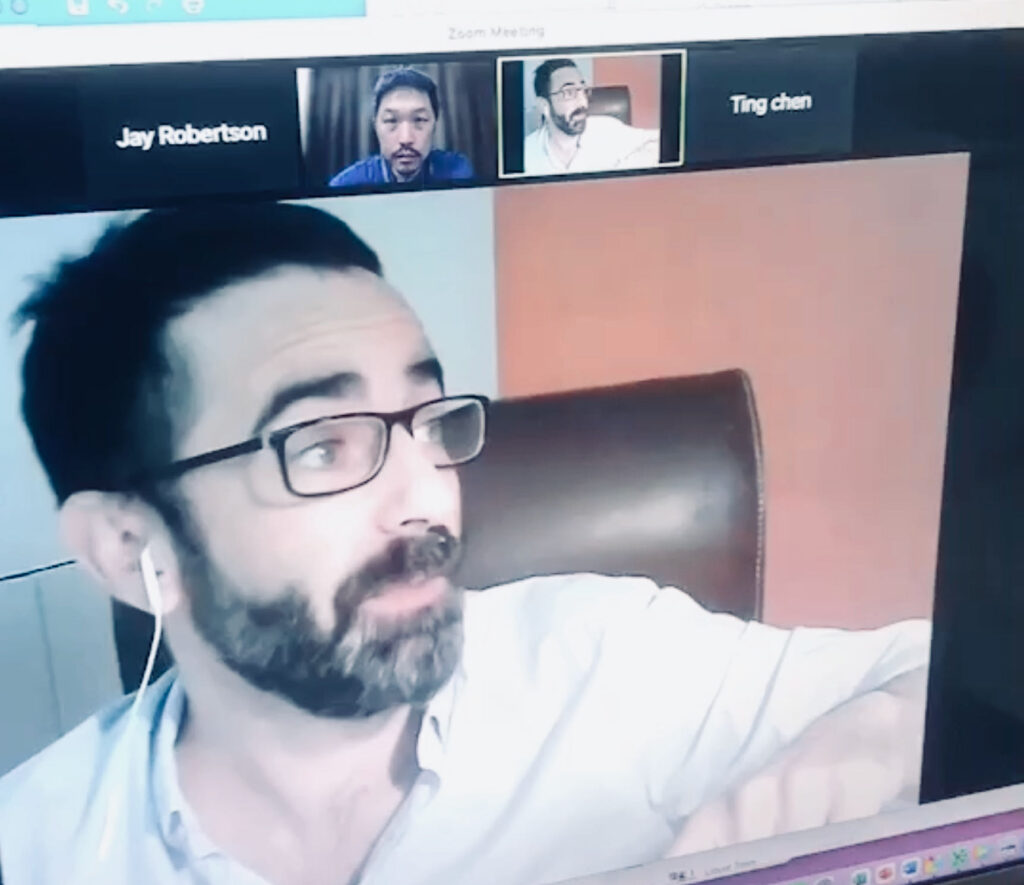
After months of meeting virtually with different architects, discussing our needs, and freeing ourselves from the unholy fetters of wearing trousers at work, we found a firm that had extensive experience in China, had a European headquarters, and was led by a whisky lover from Spain.
They were the perfect match. Alonso and Ting won us over, and we appointed SOG Design as our architects for the project.
Putting things together, brick by brick
We wanted a distinctive style, something that exudes the same timeless gravitas as some of the stunning brick buildings we’ve come across in our travels over the years – both in China and, of all places, Birmingham in the UK. The latter was to appease the head of this project, Jay, who is a proud Brummie and would have whinged for years if we didn’t include something from his home city.
We drew inspiration from brick architecture like the Shaanxi Fuping International Ceramic Art Museum, the Red Brick Art Museum in Beijing, and a few late Victorian and Edwardian buildings from Birmingham, including The University of Birmingham, Sarehole Mill, Aston Hall, and The Barber Institute of Fine Arts.
Under expert advice we were reliably informed that the best way to design a distillery was with our favourite tools: Lego, Sharpies and empty polystyrene boxes. We obviously can’t speak for everyone, but we’re pretty sure that’s how all successful distilleries start out.
We quickly moved from LEGO bricks to proper architecture for grown-ups, and the early concepts were promising. We were happy with the style and loved the overall layout. Things were moving forward quickly when we came up against our first speed bump: a little something called land utilisation ratios.
In China, every land parcel has a minimum amount of usable space that must be created for every square meter, with strict rules for how much of that space is set aside for production versus non-production. Our initial drafts were drawn up with a 1:1 ratio in mind. We had 17,000 square meters of space, so we designed 17,000 meters of distillery, complete with office space.
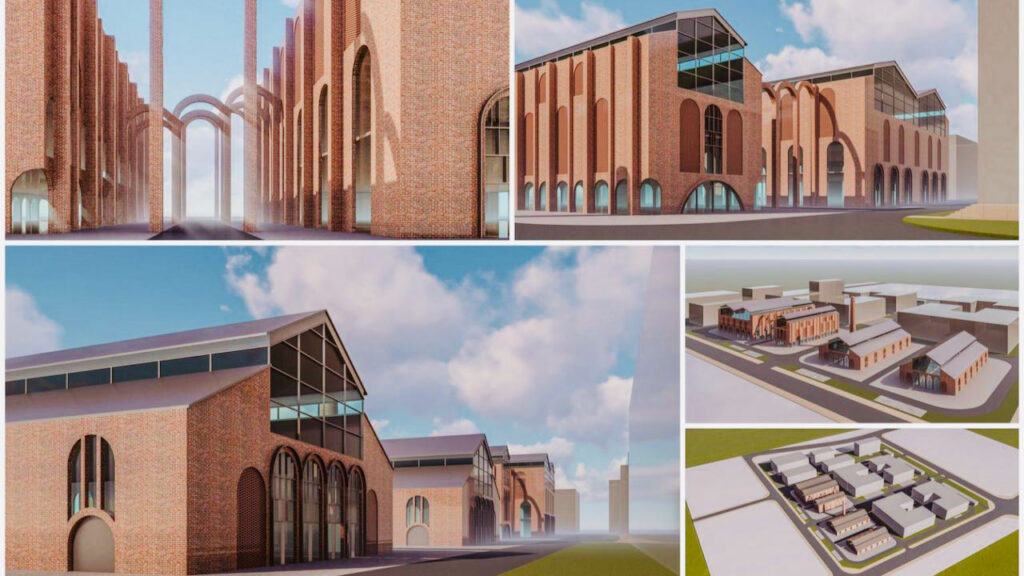
It turns out that this particular piece of land has a utilisation ratio of 1.3 – that is, for every one square meter of land, we needed 1.3 square meters of production space. That meant multiple floors, so no more fancy arches and sweeping single-storey facades. Oops.
There were all kinds of other requirements too, including accessibility for fire trucks (20 meters between each building, leaving even less room for production), emergency storage tanks for environmental risks, and tanks for roughly 1,800 tons of water that we have to keep on site at all times to supply sprinklers and fire trucks in the event of a fire.
And then there were the windows. While striking and majestic, giant glass windows aren’t the best choice for this environment. Our site is located in a subtropical zone, in Fujian province, which means we have to keep the heat out, not welcome it with open arms like they do in the chillier parts of Scotland.
We could solve this with more air conditioning, but that would violate our commitment to protecting the natural environment. So we decided to bite the bullet and design the buildings for greater thermal efficiency. More bricks, less massive windows.
It was back to the drawing boards.
When in Rome
While revamping our site design to account for land utilisation and safety requirements, we also decided it was time to consult a Feng Shui master. No, really.
Feng Shui is an ancient Chinese philosophy that prescribes certain architectural and design elements to better harmonize human spaces with their surrounding environment. While it may seem silly to some – and can be frustrating for many western architects – it’s taken very seriously in China, both in the home and in business. Good Feng Shui is seen as auspicious.
This is especially true in Fujian province, where Feng Shui is dutifully practised in most aspects of life, not least in the construction of buildings and their internal layout. With an undertaking this large (and this important to us), “when in Rome” has been our core guiding principle from day one, regardless of our individual beliefs
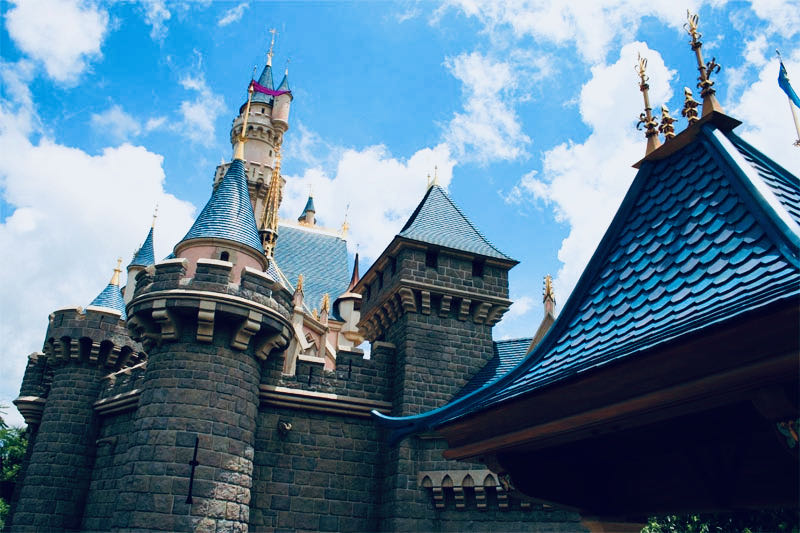
And if you think we’re silly for putting so much emphasis on what some might consider superstition… well, we aren’t the first. When building Hong Kong Disneyland, Disney execs agreed to shift the angle of the park’s front gates by 12 degrees to improve the flow of Qi into the park. This was, of course, done in response to advice from their Feng Shui master.
A happy little accident
We did end up adjusting our design based on feedback from a prominent Feng Shui master in the region, Mr. Chen Xiaoshun. Most of these were minor changes, like aligning our buildings with magnetic north, which puts them at a very slight angle relative to the rest of the site.
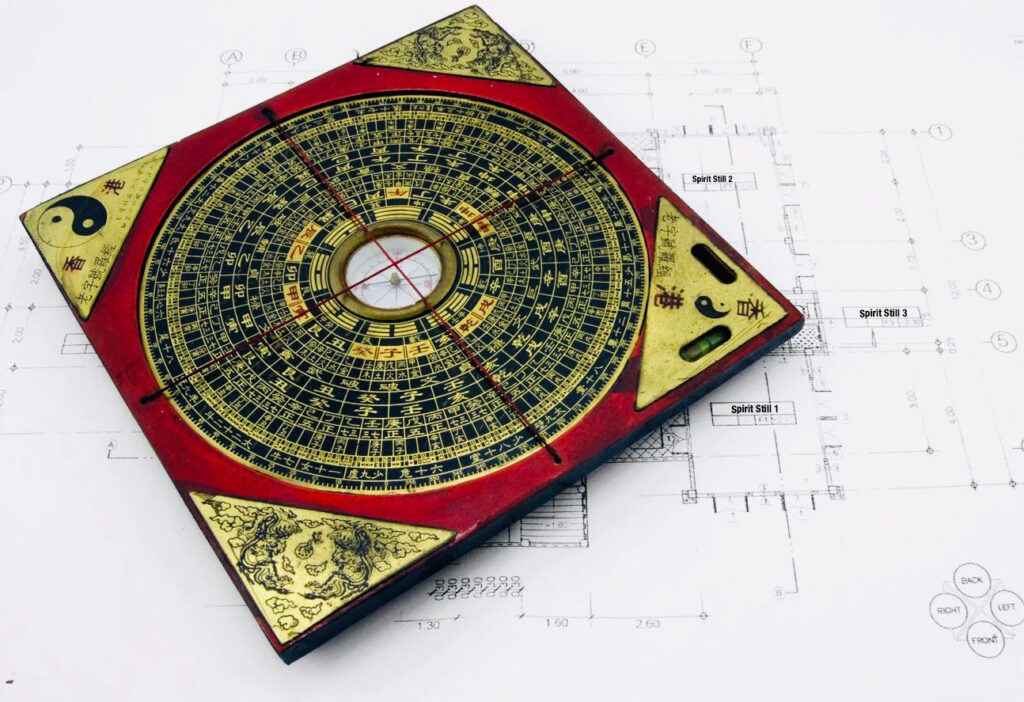
The biggest change we made was to the roofs. For good Feng Shui, the ridge on a roof should run north to south, with the planes of the roof (the roof fields) slanting towards the east and the west of the building.
This… was a problem for us. Given the shape of our land parcel, the longest side of each building runs east to west, so our roofs would have looked ridiculous.
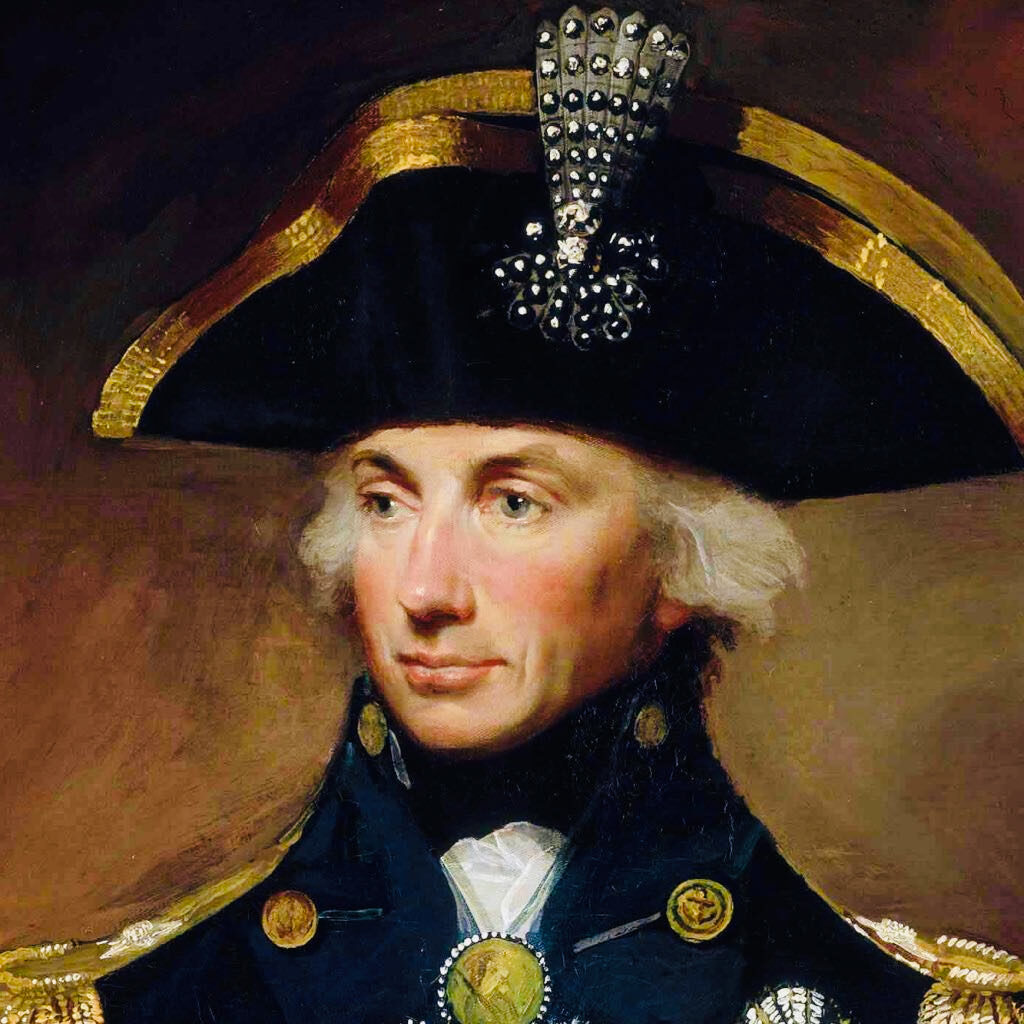
The simpler solution was to have flat roofs on all four buildings. We still have solid Feng Shui, but the buildings don’t look goofy. In fact, this design change led to a happy little accident. What our roofs would have looked like if we were 100% faithful to the principles of Feng Shui.
With flat roofs, we now have a large surface area on which we can evaporate leftover water from the distillation process. Remember what we said about protecting the environment? With this arrangement, we can take advantage of natural evaporative cooling on our roofs, which means even less energy consumption throughout the course of whisky production.
It’s a clean, environmentally friendly way of treating the byproducts of distillation.
The final design
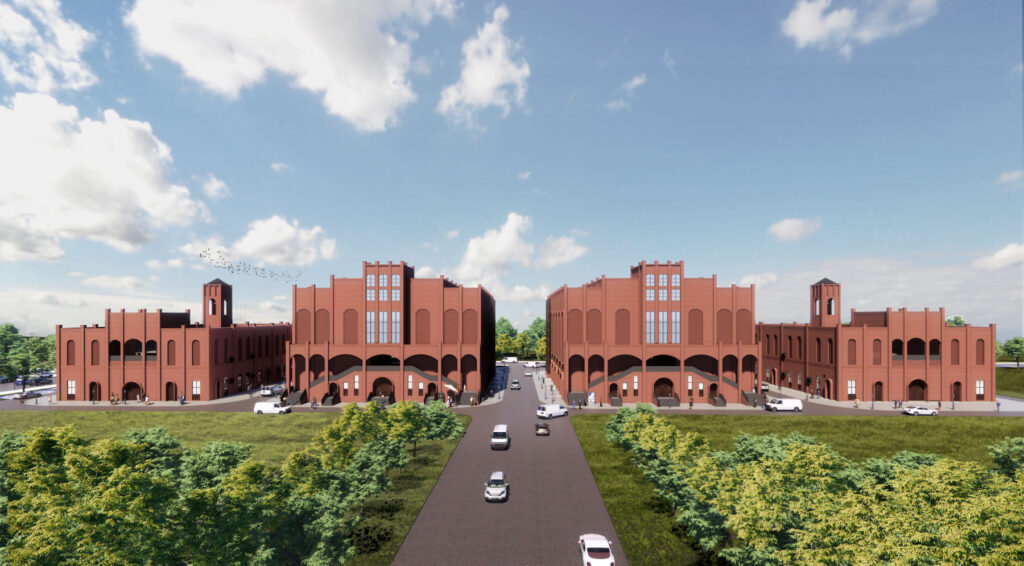
Here’s how it all turned out. The northernmost building on the right is our still house, where a lot of the magic happens. The ceilings are up to 13 meters high, allowing heat to rise and exit the building naturally, which pulls in cooler air. This, in combination with evaporation on the roofs, will greatly reduce our need for active cooling. The building on the far left is our dunnage, where we store and age our casks.
The two buildings in the middle are four storeys high, and they will be used for malting barley, milling it, and mashing it. Two whole floors will be devoted to malting alone, which will be done in the traditional method – right on the floor itself.
That’s that. We could go on for days, and probably would if you bought us a drink. In short, what began with a pile of LEGO bricks has now evolved into something real. Something grand. We got what we wanted in terms of practicality, experience, the environment, and respect for local traditions. And we can’t wait to show you around the place once everything’s up and running.
This is Part Three in a series detailing the story of Nine Rivers Distillery. CLICK HERE for Part One and CLICK HERE for Part Two.
Would You Like To Read More?
If you enjoyed reading this, and you would like to catch up with some of our past articles, then please CLICK HERE and go to our News Section, where most of our other content is published.
Follow Us
If you have enjoyed reading this and want to learn more about Nine Rivers Distillery, then use the QR Code below to follow our WeChat Official Account.
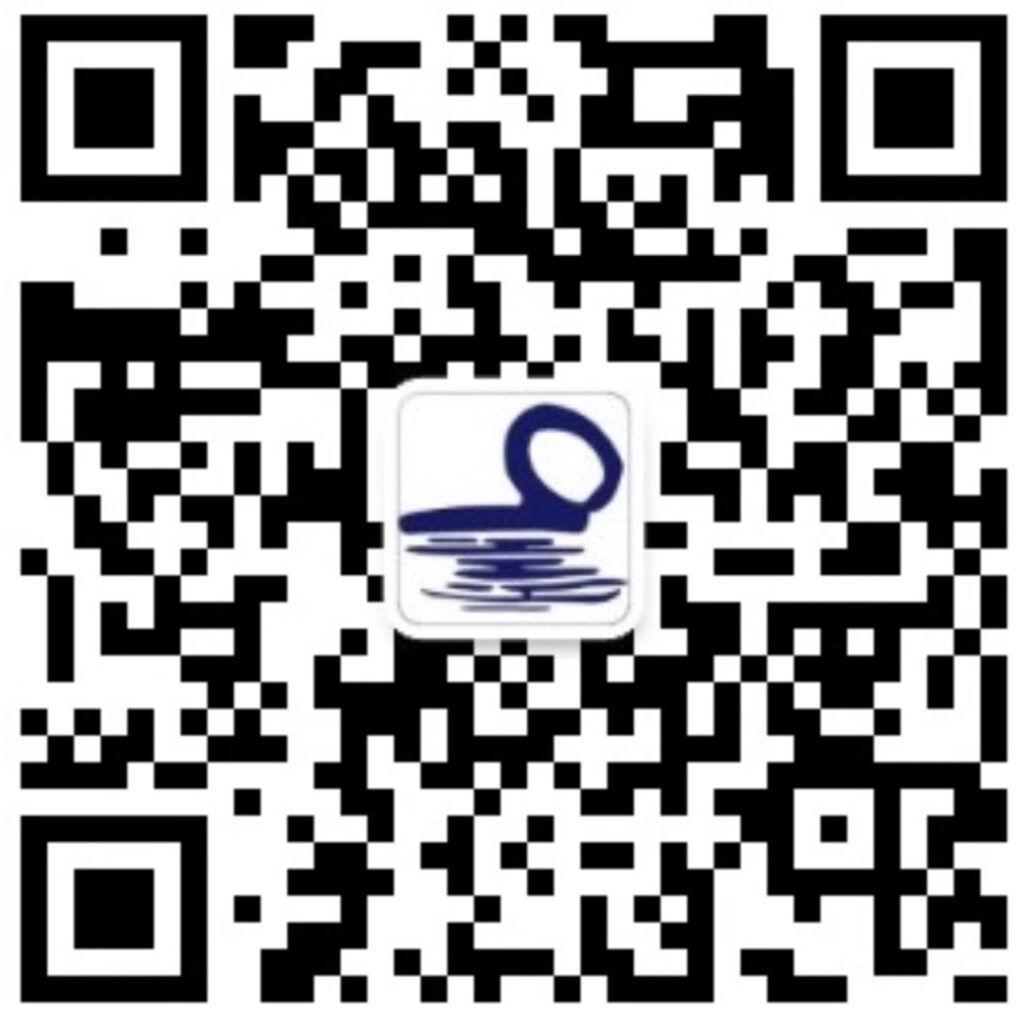
Alternatively, if you prefer Linked In then you can CLICK HERE to follow us.
Facebook users, you can CLICK HERE.